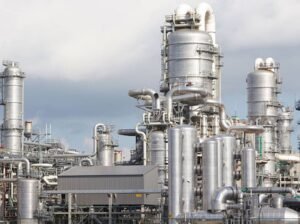
Unleashing the Power of Waste Heat Boilers: A Game-Changer for Industrial Efficiency
In the ever-evolving landscape of industrial operations, efficiency and sustainability have become paramount. Companies are constantly
Waste heat boilers provide intelligent, tailor-made solutions that enable maximum energy recovery in industrial applications. In search of higher efficiency, better fuel costs, and attainment of environmental objectives? Waste heat recovery has the answer. Let me explain how the utilization of such a system will change your operations, and how solutions designed by Gelan can enable your business.
Trusted by WORLD CLASS Companies
Why Waste Heat Recovery Should Be Your Next Investment?
Our waste heat boiler fundamentally solve three major challenges: flue gas dew point corrosion, dust abrasion, and high-temperature performance. It boasts a long lifespan, low resistance, and compact structure, allowing for reliable operation across a wide range of flue gas temperatures. This boiler is suitable for flue gas waste heat recovery systems in refinery heating furnaces, power plant boilers, and blast furnaces in steel mills. Even in harsh operating conditions, its lifespan is 3-5 times longer than that of conventional waste heat boilers, making the economic benefits evident amount of heat is released as waste.
Recovery of waste heat is not only a tool to save energy; it is an opportunity for earning money. Each drop of the waste heat fleeing your industrial processes is money that could be put to productive use. By installing a waste heat boiler, the energy can be captured and channeled into your facility.
Think about a steel mill: the heat coming off of your furnace is simply exhausted to the atmosphere unless a waste heat boiler is installed. In which case recovery of that energy drives turbines, creates steam, or supplies hot water. It’s a closed-loop system that cuts fuel costs, reduces the demand for outside energy, and improves profitability.
Key point: Waste heat recovery impacts operational cost, profit margin, and sustainability…
Making the right selection of waste heat boilers can bring in increased efficiencies and savings unparalleled before. Each of the waste heat boilers from Gelan is specifically engineered for industrial applications at your plant, since each has very specific needs, for maximum return on investment.
Based on their structure, there are mainly two major types of waste heat boilers: shell and tube, and others. They consist of either a tube bundle or coil heat exchanger. Inside the heat exchange tubes, the process media are circulating, while the shell is filled with cooling water. The heat coming from the process media heats and boils the cooling water to produce steam. Based on two different criteria, these boilers may further be classified into two subgroups:
Based on the structure, the other main type of waste heat boiler is the flue gas waste heat boilers. These are modular steam generators using high-temperature flue gases for heating the water and consequently producing steam. They find their application in chemical furnaces and comprise vertically arranged heat exchange tubes to transfer the heat from flue gases to the water inside the tubes. The steam thus produced may be used for different industrial applications.
Coking plants produce a large amount of coking waste gas at 550-900°C during coking production. In order to further recover the coking waste gas
Automatic coke oven gas burner is adopted, where coke oven gas is burned inside or outside the waste heat boiler and then mixed with coking waste gas to form high temperature flue gas into the boiler for heat exchange to produce rated steam. Low cost, small footprint and high efficiency, environmental protection,In factories, printing and dyeing, chemical and other industries in the production of toxic and hazardous gases, extremely harmful to the environment, these exhaust gases contain organic gases, sulfides, phenols, harmful gases, the general choice of incineration, the use of direct combustion furnace (TO furnace), regenerative combustion furnace (RTO), catalytic combustion furnace (RCO).
After incineration, the waste heat is recovered and cooled down to meet the temperature requirements of desulfurization and denitrification, which can realize the double role of environmental protection and energy saving.Carbonaceous raw materials (anthracite coal, petroleum coke, etc.) are calcined at high temperature under the condition of air insulation is the first process of carbonaceous production, and the high temperature flue gas discharged in the process of calcination can be reused as waste heat. According to the actual situation of waste heat resources, our company has configured different specifications of waste heat steam boiler or waste heat organic heat carrier furnace. Energy saving, cost saving
An investment in a Gelan waste heat boiler offers numerous key financial benefits to any company
The flue gas inlet section is equipped with anti-abrasion devices to ensure the safety of the windward tube bundle.
The material for the low-temperature section tube bundles is selected from our proprietary composite alloy pipes combined with soft enamel structures, ensuring overall corrosion resistance and durability.
The compact structure occupies less land area and space, typically reducing the volume by about 20% compared to traditional waste heat boilers. It utilizes a modular design for flexible application, allowing adjustments to fit the size of the heating furnace, which facilitates transportation and installation.
High heat transfer performance; our company uses imported finned tube production lines with a high-frequency resistance welding fusion rate. The fin welding rate exceeds 98%, resulting in low thermal resistance. The heat transfer performance per unit length of our finned tubes can improve by about 10% compared to domestic alternatives.
Cost-effective; with a high overall cost-performance ratio and significant energy savings, the tail section of the heating surface equipped with our newly developed waste heat boiler can enhance the overall thermal efficiency of the heating furnace by 6% to 20%. The investment payback period can be recouped in a short time.
We have multiple successful cases covering various industrial sectors, such as petrochemical, metallurgy, and hydrogen production. These cases highlight the significant benefits of waste heat boilers in improving energy efficiency, reducing emissions, and saving costs.
Cyprus 12 Million Tons Per Year Refinery Hydrogen Production Unit Waste Heat Boiler (Including 70-Meter Steel Chimney)
Philippines efinery Phase II 10 million tons per year atmospheric distillation unit, atmospheric heating furnace, and vacuum heating furnace (including waste heat recovery).
Indonesia Refinery : 1.8 Million Tons per Year Catalytic Reforming Unit – Integrated Reforming Heater and Waste Heat Boiler
Need a free solution? Your dedicated engineer, Mr. Richard, will contact you within the hour to provide a comprehensive and economical project cost report based on your project needs.
We do not share your personal information with third parties. By clicking the button, you consent to the processing of personal data.
Waste heat recovery recaptures the energy from waste heat generated in industrial processes and makes it serve a valuable purpose, such as steam or power generation.
The systems for recovering waste heat circulate hot exhaust gases through the inlet of a waste heat boiler to transfer energy into water or steam, which in turn feeds into various industrial applications. The recovered energy reduces additional fuel consumption, hence increasing efficiency.
Waste heat boilers recover heat from the spent gases to produce either steam or hot water. The system reuses the energy that is usually wasted and brings efficiency to industrial systems.
Designing of the waste heat recovery boiler depends on certain parameters or factors that include the temperature in the exhausts, composition of gases, and energy requirements at the process site. Since designs are made to order, the energy recovered is maximum, hence assuring efficiency in operations peculiar to each process.
Please note that the final cost depends on the customized service you require, the specifications of the raw materials used, the relevant national laws, and the distance of transportation. Take the example of booking a tall container of products:
In the ever-evolving landscape of industrial operations, efficiency and sustainability have become paramount. Companies are constantly
Fired heaters are great for heating large spaces like buildings, plants, or work zones, and they
If you need something to help warm up a vast space like a workshop, factory, or
Underground water tanks are a great way to store water while keeping your yard or space
A gasketed plate heat exchanger is a helpful tool that moves heat between two liquids using
Ethylene is used in many things, such as plastic and fuel. To make ethylene, you must
When big factories and power plants work, they make a lot of extra heat. Most of
Boilers make heat, but not all of that heat gets used. A lot of it goes
Heat is significant in machines and big systems. When heat moves fast, it saves power and
Buying a new furnace can cost a lot of money. But don’t worry, because there are
Feel free to get in touch with us!
We will contact you within 1 hours, please pay attention to the email with the suffix “@gelanpetro.com”.
We are pleased to receive your letter and help you achieve your business goals. Fill in the form below to send us information or talk directly to our product experts by phone.